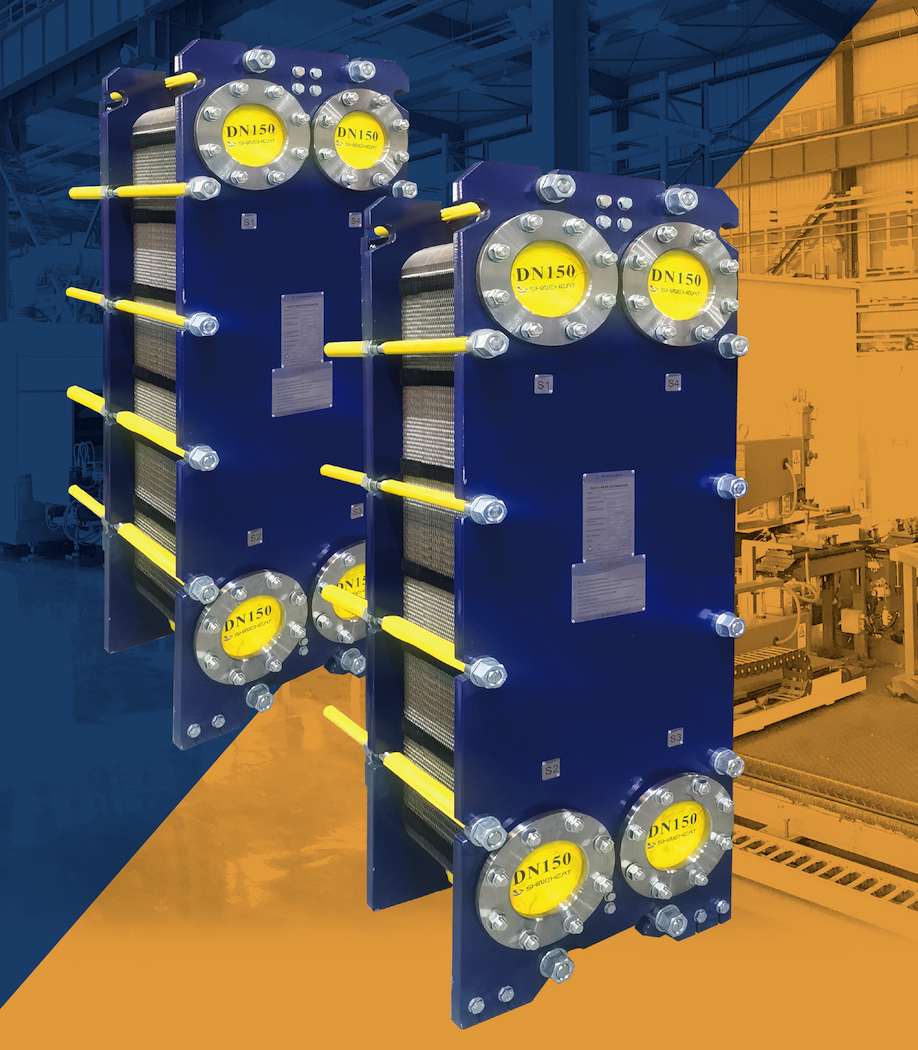
What is “Heat Transfer”?
Heat transfer is a discipline of thermal engineering that concerns the generation, use, conversion, and exchange of thermal energy (heat) between physical systems. Heat transfer is classified into various mechanisms, such as thermal conduction, thermal convection, thermal radiation, and transfer of energy by phase changes. Engineers also consider the transfer of mass of differing chemical species, either cold or hot, to achieve heat transfer. While these mechanisms have distinct characteristics, they often occur simultaneously in the same system.
(From Wikipedia)
The theory of heat transfer is going to find out the energy transfer that may take place between material bodies because of temperature difference. This energy transfer is regarded to thermal heat. The three modes by which thermal heat can be transferred from one place to another
- Conduction
- Convection
- Radiation
What is a Plate Heat Exchanger?
We understand how “Heat Transfer” Happen, now we come to know what is a Plate Heat Exchanger’s work principle, How does a Plate Heat Exchanger work?
The thermal heat is transfer by “Conduction” through a thin corrugated metal plate from one fluid to another fluid, and the two fluids are flowing spread out cover the metal plate by counter flow.
The two fluids flow separately inside of Plate Heat Exchanger, they are not contact or interference each other, they have their own flow route or passage. Numbers of routes or passages are forming inside of Plate Heat Exchanger; they are seal by Gaskets or Welding Seams. The main components of Plate Heat Exchanger are
- Corrugated Plates for thermal heat transfer
- Gaskets or Welding Seams for flow routes seal
- Frame and Fasten Bolts for pressure undertake
A Brief History of the Plate Heat Exchanger
Introduction:The plate heat exchanger, also known as PHE, is an integral component of modern heat transfer systems. Its invention and development have revolutionized industries such as HVAC, power generation, chemical processing, and food and beverage production. we will provides a historical overview of the plate heat exchanger's development, highlighting key individuals and manufacturers involved in each stage.
Early Concepts and Prototypes (mid-1800s to early 1900s):
The concept of a plate heat exchanger began to take shape in the mid-1800s when experimentation with heat transfer emerged. Francois Marie Raoult conducted early work on plate heat exchangers, but it was Carl Richard Nyberg who is credited with the first practical plate heat exchanger design in 1923.
Industrial Application and Advancements (1930s - 1950s):
In the 1930s, Tranter Inc., a leading heat transfer equipment manufacturer, began producing gasketed plate heat exchangers, significantly advancing the technology. Tranter's design featured a gasket seal between individual plates, allowing for easy maintenance and enhanced thermal efficiency.
Evolution of Gasketless Plate Heat Exchangers (1960s-1970s):
The 1960s marked a significant milestone with the introduction of gasketless plate heat exchangers. Manufacturer Alfa Laval played a vital role in this period, developing the first gasket-free plate heat exchanger in 1960. Alfa Laval's design utilized a brazed sealing process, eliminating the need for gaskets and providing improved heat transfer capabilities.
Introduction of Laser Welding and Compact Designs (1980s-1990s):
In the 1980s, laser welding technology made its way into the plate heat exchanger manufacturing process. This advancement allowed for tighter, more secure welds, ensuring better heat transfer efficiency. Kelvion, formerly GEA Ecoflex, is a notable manufacturer that embraced laser welding technology during this period, contributing to the compact design evolution of plate heat exchangers.
Innovations in Materials and Applications (2000-present):
In recent decades, advancements in material technology have expanded the range of applications for plate heat exchangers. Manufacturers such as Danfoss and SWEP have introduced stainless steel and corrosion-resistant alloys, allowing for broader use in demanding industries like offshore oil and gas. Additionally, improved design software and computational fluid dynamics have enabled more accurate sizing and customization of plate heat exchangers for specific applications.
Conclusion:The plate heat exchanger has come a long way from its early concepts and prototypes to its current state as a highly efficient, versatile, and widely used heat transfer solution. Throughout its development, key individuals such as Carl Richard Nyberg, Alfa Laval, Tranter Inc., Kelvion, Danfoss, and SWEP have played pivotal roles in enhancing its performance, efficiency, and range of applications. As technology continues to evolve, the plate heat exchanger will undoubtedly remain an essential component of modern heat transfer systems.
How many types of plate heat exchanger are there?
In view of different type Seal method, the plate heat exchanger could be classified into following categories
- Plate and Gasket Heat Exchanger
- Welded Plate and Frame Heat Exchanger
- Semi-Welded Plate Heat Exchanger
- Brazed Plate Heat Exchanger
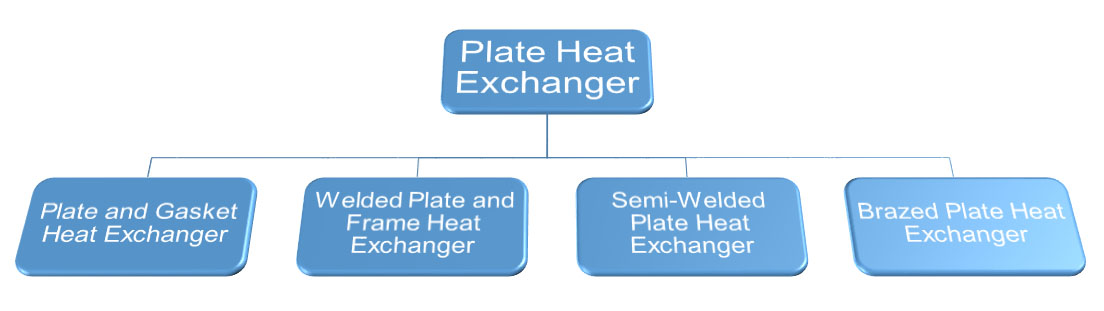
In view of different working applications, the plate heat exchanger could be classified into following categories
- Plate Evaporator
- Plate Condenser
- Wide Gap Plate Heat Exchanger
- Double Wall Plate Heat Exchanger
- Free Flow Plate Heat Exchanger
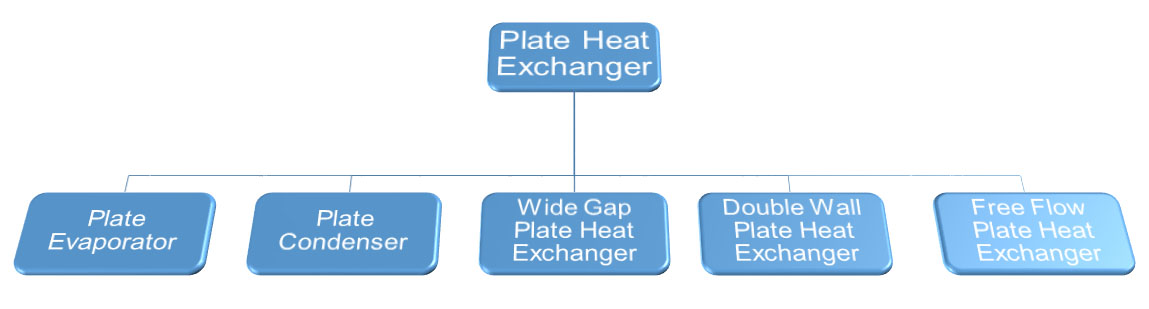
Classification of Plate Heat Exchangers Based on Structure and Applications
Plate heat exchangers are widely used in various industries for their compact size, high heat transfer efficiency, and versatility. We classify plate heat exchangers based on their structure and applications, providing an overview of each category and highlighting their distinct features.
Gasketed Plate Heat Exchangers:
Gasketed plate heat exchangers are the most common type, offering flexibility and easy maintenance. They consist of a series of corrugated plates with gaskets between them, forming alternating channels for the hot and cold fluids. The gaskets ensure a reliable seal, preventing leakage. These heat exchangers are suitable for a wide range of applications such as HVAC, food and beverage processing, and chemical industries.
Brazed Plate Heat Exchangers:
Brazed plate heat exchangers are compact and efficient, designed for higher pressure and temperature applications. The plates are made of stainless steel or other high-grade materials, brazed together using copper or nickel. The brazing process eliminates the need for gaskets and enhances the heat transfer efficiency. These heat exchangers are commonly used in refrigeration, condensing boilers, and industrial processes.Welded Plate Heat Exchangers:Welded plate heat exchangers are suitable for more demanding applications, where high pressures and temperatures are involved. The plates are welded together, forming a robust and leak-proof structure. As a result, these heat exchangers can handle aggressive fluids, making them ideal for chemical processing, oil and gas, and power generation industries.
Semi-Welded Plate Heat Exchangers:
Semi-welded plate heat exchangers combine both gasketed and welded designs. One fluid path utilizes gaskets, while the other path has welded plates to withstand more challenging conditions. These heat exchangers offer versatility, as they can handle fluids with varying temperature and pressure differentials. They find applications in HVAC, industrial cooling, and heat recovery systems.
Wide-Gap Plate Heat Exchangers:
Wide-gap plate heat exchangers feature larger plate spacings, allowing for the transfer of viscous or particles-laden fluids. The wider gaps prevent clogging and fouling, making them suitable for applications such as wastewater treatment, pulp and paper processing, and mining industries.Conclusion:Plate heat exchangers are categorized based on their structure and applications, each serving different needs in various industries.
The gasketed, brazed, welded, semi-welded, and wide-gap plate heat exchangers offer distinct benefits and are choiced based on factors like pressure, temperature, fluid characteristics, and space limitations. Understanding the classification of plate heat exchangers enables engineers and industries to choose the most suitable solution for their specific requirements, ensuring efficient heat transfer and optimal system performance.
Plate and Gasket Heat Exchanger is most common type of Plate Heat Exchanger, which has a flexible design, are easy to service, and maintain. The product range is extremely wide and is used in duties for heating, cooling, heat recovery, evaporation and condensation in industries ranging from HVAC, refrigeration, engine cooling, dairy and food to heavier processes like chemical processing, oil production and power generation.
How does a Plate Heat Exchanger work?
The gasketed plates are assembly into a Plate Pack, mounted on Upper and Lower guide bars, and compressed by two end frames with fasten bolts. Heat Exchanger Fluid flow in and out through end fame connections and are distributed to pass through the corrugated plates. The flow is controlled by alternate placement of port gaskets, while the Hot Fluid or Cold Fluid flows in the opposite direction on the other side of the plate. The temperature difference created by these opposite flows results in the closest temperature approach for maximum heat transfer efficiency.
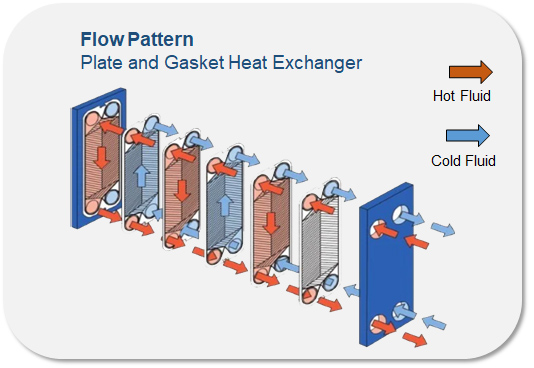
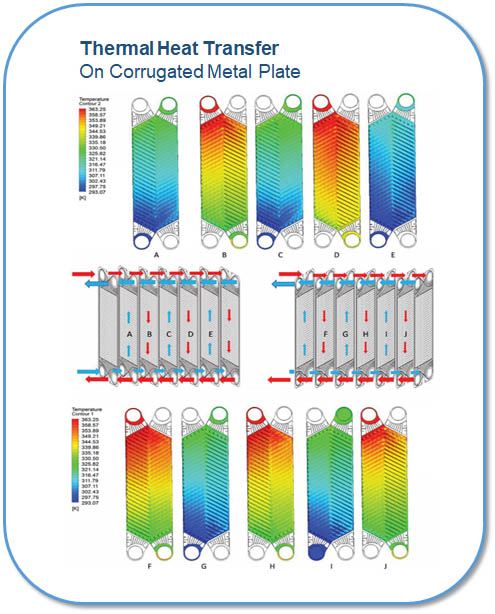
Plate and Gasket Heat Exchanger provide efficient heat transfer in compact equipment with a small footprint. The units have a flexible design and are easy to service and maintain. The product range is extremely wide and is used in duties for heating, cooling, heat recovery, evaporation and condensation in industries ranging from HVAC, refrigeration, engine cooling, dairy and food to heavier processes like chemical processing, oil production and power generation.
Features for Shineheat Plate Heat Exchanger
Professional Frame Fabrication for Plate Heat Exchanger
CNC cutting for fame, warranty frame size exactly accuracy (less than 2mm size deviation)
Sandblasting for First fame Coating, then three ground coat paints, one finishing paint.
Roller Bearing make movable frame easier for assembly
Special Process Coating in Carry Bar for better Anti-Corrosion


Widely Option for Plates Patterns for Plate Heat Exchanger
150 Type Plate Models Cover Most Regular OEM Plates Patterns,
Transfer Area from 0.032~3.96 m2/P, Connection Size from DN32-DN500
The Most Optimal Solution by Premium Plates Design among various suppliers
Large Availability for Service Replacement Spare Parts, one-stop procurement
Flexible Connections for Plate Heat Exchanger
SS316L Studded Lining Connection with Matched Flange
Welded Nozzle Connection with Matched Flange
ASME Standard Boosted Connection
All Optional Connection Standard (ANSI, DIN, PED, GB)
Plate Heat Exchanger Frame Expandable
Our standard Frame Capacity Margin is 30% by adding extra Plate; Enough Frame Margin will also contribute to convenience for plate removing;
Customized Frame and Connection design for special workspace
When the Operating Space is Limited, we design Compact Frame Structure to save space. Even in replacement Job, we would recalibrate connections and reduce extra pipeline work.
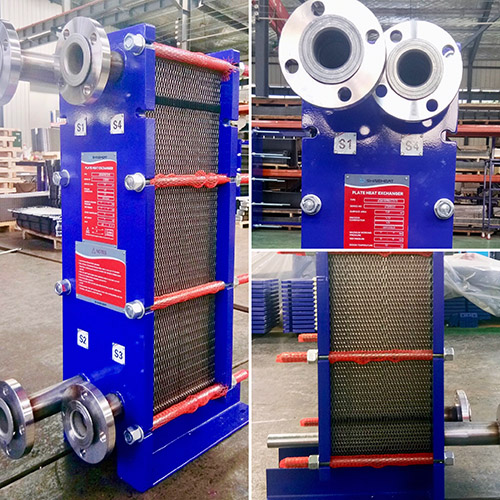
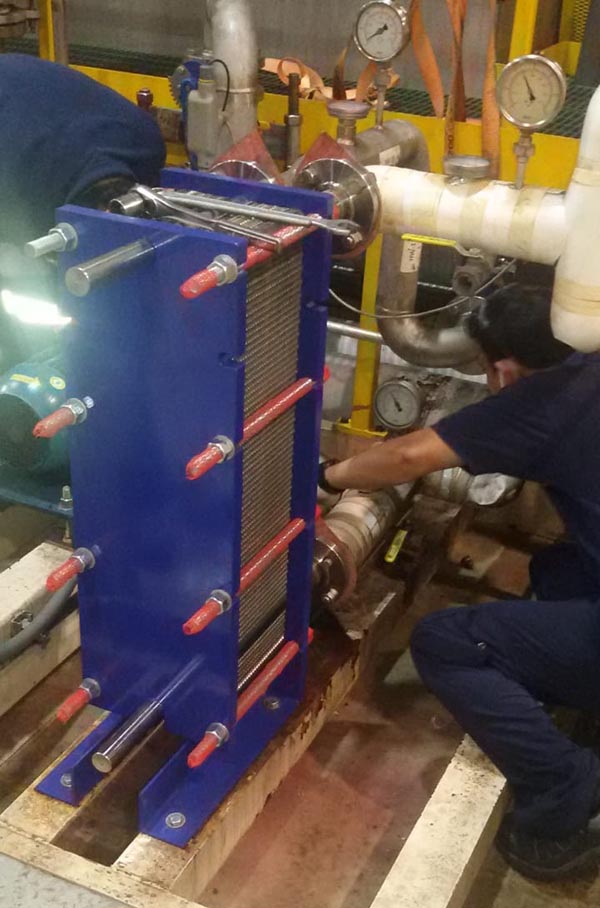
Optional for Frame Material Variety
For Sanitary or Diary industries, Stainless Steel Frame and accessories is required for Frame Material. Now we could offer
Solid Stainless Steel Frame SS304 or SS316L
Carbon Steel Coating Stainless Steel SS304 or SS316L
Extended Line for Plate and Gasket Heat Exchanger
Free Flow/Wide Gap Plate Heat Exchanger
SHINEHEAT Free Flow Plate Heat Exchanger, which deigned with a wider fluid-flow Channel, Making it ideal for viscous fluids, slurries, and effluent streams that contain particles and fibers that could block the flow channels. Furthermore, two fluids are individually gasketed sealing, make it possible for operating where product contamination can’t be tolerated.
Like frame and gasket heat exchanger, Free Flow Plate Heat Exchanger is in compact structure, easy to dismountable and clean. Capacity expansion also could be realized.
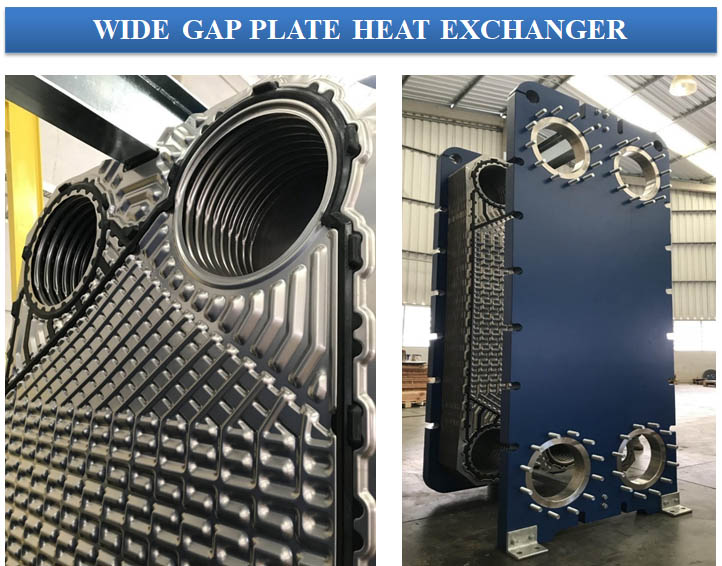
CE Certified Plate Heat Exchanger is available for optional request