Mastering the Art of Titanium Plate Heat Exchanger Welding
Welding titanium plate heat exchangers is a special process that demands precision, expertise, and advanced equipment. Given the thin nature of titanium plates, often ranging from 0.8mm to 1.0mm in thickness, traditional non-destructive testing methods like RT and MT become impractical. Consequently, the welding process relies heavily on skilled technicians and well-established procedures.
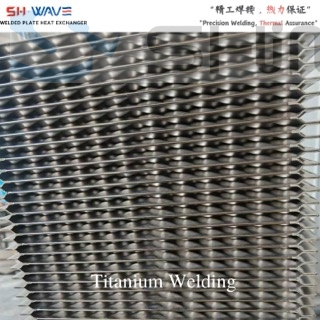
The Challenges of Titanium Welding
Titanium welding presents a unique set of challenges due to its reactive nature and the thinness of the plates. Some of these challenges include:
- Susceptibility to contamination: Titanium readily reacts with oxygen, nitrogen, and other elements, forming brittle compounds. This makes it essential to maintain a clean and inert welding environment.
- Heat sensitivity: Titanium is susceptible to distortion and cracking at high temperatures. Therefore, precise control of welding parameters is crucial.
- Thin plate thickness: Welding thin titanium plates requires professional equipment and techniques to prevent burn-through and ensure a strong, leak-tight joint.
SHINEHEAT: A Expert in Titanium Plate Welding
SHINEHEAT has developed a deep understanding of the complexities involved in welding titanium plate heat exchangers. Through years of experience and continuous improvement, we have perfected a welding process that consistently delivers high-quality results.
Key Elements of Our Welding Process
- Advanced Laser Welding Equipment: We utilize state-of-the-art laser welding equipment, specifically designed for thin-gauge metals. This equipment allows for precise control of the welding process, resulting in minimal heat input and reduced distortion.
- Specialized Welding Procedures: Our welding procedures have been meticulously developed and refined to ensure optimal weld quality. We carefully control parameters such as welding speed, power, and shielding gas flow to achieve consistent results.
- Stringent Quality Control: Every welding operation is subject to rigorous quality control measures. We employ a combination of visual inspection, dimensional checks, and non-destructive testing methods to verify weld integrity.
- In-House Testing: To further validate our welding processes, we regularly submit weld samples to third-party laboratories for comprehensive testing. This enables us to fine-tune our procedures and ensure ongoing compliance with industry standards.
Tailored Solutions for Diverse Applications
SHINEHEAT offers customized welding solutions to meet the unique requirements of various industries and applications. Our expertise extends to welding titanium plates of different thicknesses and with varying wave patterns, ensuring optimal performance in a wide range of operating conditions.
Benefits of Choosing SHINEHEAT
- Superior Weld Quality: Our advanced welding techniques and rigorous quality control ensure that our titanium plate heat exchangers meet the highest industry standards.
- Customized Solutions: We work closely with our customers to develop tailored solutions that meet their specific needs.
- Short Lead Times: Our efficient manufacturing processes and streamlined supply chain enable us to deliver products on time.
- Global Reach: We serve customers worldwide, providing expert support and reliable service.
SHINEHEAT is committed to providing the highest quality titanium plate heat exchangers. Our expertise in welding technology, coupled with our state-of-the-art equipment, enables us to deliver products that meet the most demanding industry standards.