SP-Wave made its tiny contribution to fight against Climate Change
SP-Wave made its tiny contribution to fight against Climate Change
The Project Introduction:
The Project Owner, OMNI Conversion Technologies Inc. had lunched the first commercial plant in production which use unsorted non-recyclable Municipal Solid Waste (MSW), which is currently disposed of in landfills, to produce negative carbon H2 in California.
The Contractor, Macrotek Inc., is to design and supply a Gas Quality Control System (GQCS) for OMNI Conversion Technologies Inc. (OMNI CT) for their unprecedented waste to H2 product. Macrotek’s GQCS will include its proprietary SULFCAT® technology which recovers contaminants to produce negative carbon by-products. New technologies are essential in the fight against climate change.
The supplier, Shineheat Tech supplied SP-Wave Spiral Plate Heat Exchanger to Macrotek as Process Liquid Cooler for Macrotek’s GQCS
For ASME U Stamp Qualification:
The ASME U Stamp certified production is obligatory when delivery to North America, so the Shineheat had been compliance with ASME standard from Design, Material, Manufacture and Inspection all aspects.
The main key issue for AMSE production execution
1. Raw Material, Main components of production should be in line with ASME SA standard, the certification need review and approval by appointed ASME Engineer.
2. Stress Analysis, All the main components need to Scientific modeling and computing, also include Spiral Plates; Unlike other standard, it is a little challenge to make stress analysis for thin Spiral Plates by considering of material cost.
3. Inspection, the Inspection and Test Plan had reviewed and approval by ASME Engineer prior to production. So each step inspection need to solid proof for execution, furthermore, the hydraulic test had done by Nitrogen Gas and water for two sides with four times, First two-time goes to Welded Plate Coil, another goes to completed unit.
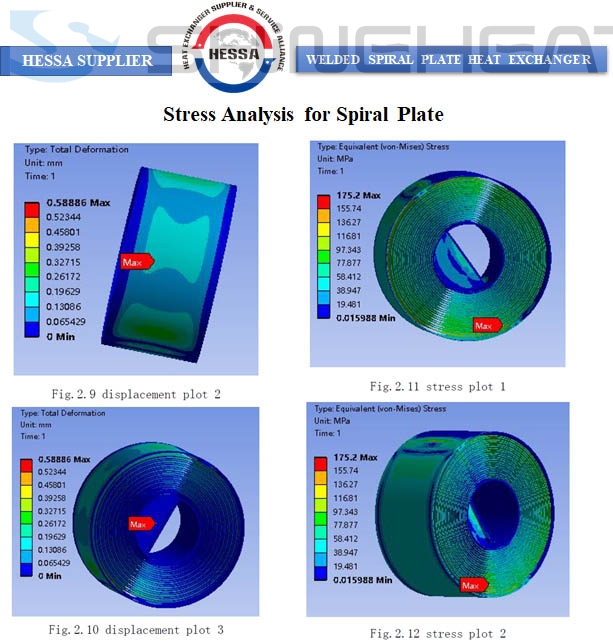
The Highlights for SP-Wave Spiral Plate Heat Exchanger Structure
1. Well Interface Connection, Paralleled Head-bonnet design make interface connections in well arrangement, and easier for Spiral Plate Heat Exchanger installation on site.
2. Flat Cover Rotation Device make Spiral Plate Heat Exchanger more safety and easier to open the dismountable cover during service on site.
3. Reinforced Support between Plates are dually internal strength in SP-Wave Spiral Plate Heat Exchanger.
4. SP Special Rolling Reinforce Device will perform its function when Plate rolling with thousands of Pins, it is also key of “IP” for SP-Wave Spiral Plate Heat Exchanger